Production of the BMW iX5 Hydrogen has begun in the BMW Group’s pilot plant located at its Munich Research and Innovation Centre (FIZ). During the development phase, the world’s first ever Sports Activity Vehicle (SAV) equipped with hydrogen fuel cell technology has already finished a rigorous testing programme under demanding conditions. Beginning in the spring of 2023, this SAV will be used as a technology demonstrator for carbon-free mobility in certain regions.
According to Frank Weber, a member of the BMW AG Board of Management involved in the development, hydrogen is a versatile energy source that will play an essential role in BMW’s Development toward its goal of becoming carbon neutral.
Because BMW is confident that hydrogen will soon play a significant role in individual mobility, the company believes that a combination of battery and fuel cell electric drive systems will be the most effective strategy in the long run. Because fuel cells don’t require any vital rare earth resources like cobalt, lithium, or nickel, the company can increase the BMW Group’s geopolitical resilience by investing in this drive system. The automaker will be able to obtain fresh and valuable insights with the help of the BMW iX5 Hydrogen test fleet, which will enable the company to provide customers with an attractive product range once the hydrogen economy becomes a widespread reality.
According to Milan Nedeljkovi, another member of the BMW AG Board of Management involved in the development, the manufacturing of the BMW-developed fuel cell systems and the BMW iX5 Hydrogen display the company’s great flexibility and unmatched know-how in the field of small-scale manufacture. He goes on to say that this demonstrates that the organisation already possesses the necessary competence to include hydrogen technology into the production system of the BMW iFACTORY as an extra type of drive.
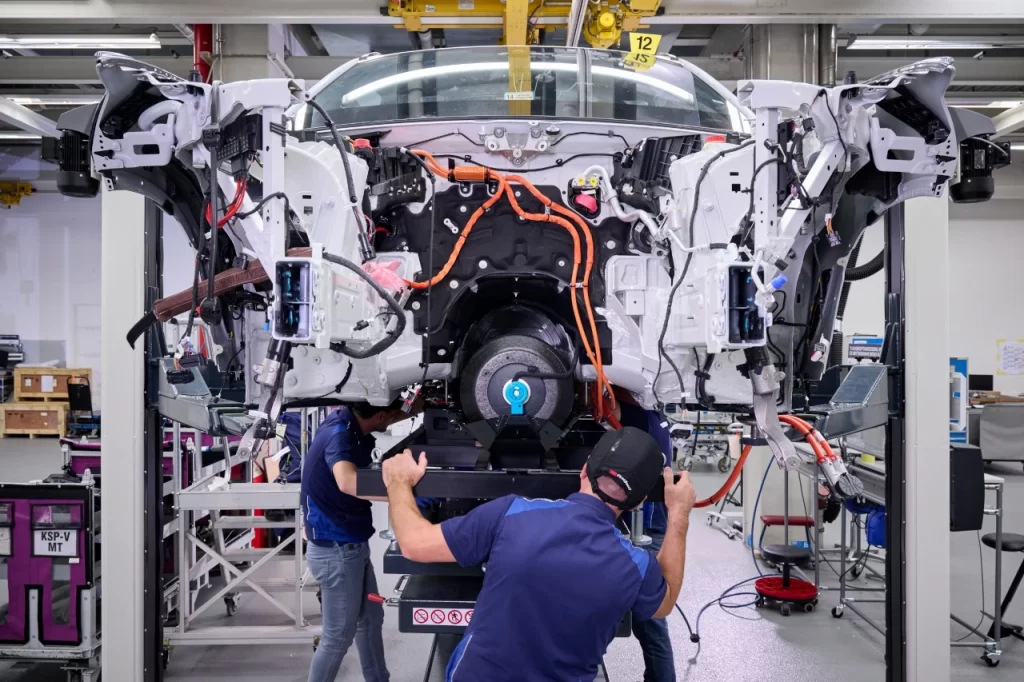
Every new model that is released by any of the company’s brands goes through its first stages of production at FIZ, which serves as the interface between product development and production. In the body shop, assembly, model engineering, manufacturing of concept vehicles, and additive manufacturing, there are roughly 900 personnel. They are responsible for guaranteeing that the product and the manufacturing process are ready for serial production on as many as six vehicle projects simultaneously. Experts in hydrogen technology, vehicle development, and the early assembly of new models worked closely together to develop the cutting-edge drive and energy storage technology that was incorporated into the BMW iX5 Hydrogen.
BMW Group Plant Spartanburg in the United States supplies the base cars for the BMW X5-platformed hydrogen variant. The pilot plant’s body shop equips them with a redesigned floor assembly that allows the two hydrogen tanks to fit the rear seat assembly and in the centre tunnel. During the assembly phase, in addition to the basic manufacturing components, model-specific components such as the 12V and 400V electrical systems, high-electric motors, performance batteries, and fuel cells are integrated. The high-performance battery and the electric motor are both positioned in the back axle region of the vehicle. The electric motor is a product of the current generation of BMW eDrive technology, which is the fifth generation. This technology is also utilised in BMW battery electric vehicles and BMW plug-in hybrid vehicles. Since August of this year, the fuel cell systems installed under the hood of the BMW iX5 Hydrogen have been built at BMW’s in-house hydrogen competence centre in Garching, north of Munich.
Numerous components are manufactured exclusively for the hydrogen-powered SAV, including some manufactured at the Additive Manufacturing Campus – the BMW Group’s 3D printing expertise hub – which is also a part of the pilot plant. Each BMW iX5 Hydrogen goes through all of the regular production processes, starting in the body shop, continuing to the paint shop, and ending with an inspection of the vehicle’s overall quality. After this, each vehicle is sent to the testing centre of the BMW Group, which is located in Aschheim, to undergo an exhaustive operational inspection.
As per the company, the BMW iX5 Hydrogen combines the benefits of an emission-free driving system with great day-to-day usability and the capacity to travel for long distances. As a result of this, its hydrogen fuel cell technology presents an intriguing alternative to battery-powered electric driving systems. This is especially relevant for customers who require brief refuelling pauses but must travel long distances and for locations that still need adequate charging infrastructure.