By the late 1990s, it was evident that the PS-90A turbofan engine had no further development prospects, owing chiefly to its out-of-date compressor, which dated back to the first Perm jet engine, the D-20P, built in the 1960s. As a result, between 1999 and 2000, Aviadvigatel JSC, led by A.A. Inozemtsev, created a new generation 5+ gas generator. This gas generator included a five-stage high-pressure compressor with a pressure ratio of 11, an annular combustion chamber, and a single-stage cooled turbine. This universal gas generator was intended to serve as the base for a series of turbofan engines, including the PS-7 (71.6 kN thrust), PS-9 (100 kN thrust), PS-14, PS-18, and several more powerful engines.
In 2002, the preliminary design of a new Russian medium-haul aircraft known as the MS-21 or MC-21 in Russian (Mainline Aircraft of the 21st Century) was finished. The new aircraft was intended to supplement the regional jet RRJ (now SSJ), which was in the latter stages of development, and to compete with the Western Airbus A320 and Boeing 737.
At that point, it was evident that the new MS-21 aircraft required a new Russian engine. The Central Institute of Aviation Motors (CIAM) and Aviadvigatel JSC in Perm created a technical profile for a potential turbofan engine with a direct drive fan, and in 2004, the program to lay the scientific and technological groundwork for its development began. The engine was given the designation PD-14 (Promising Engine with 14-ton thrust). Meanwhile, the American PW1400G turbofan engine was chosen to power the MS-21.
The first flight of the MS-21-310 (series No. 005) with PD-14V engines took place in December 2020.
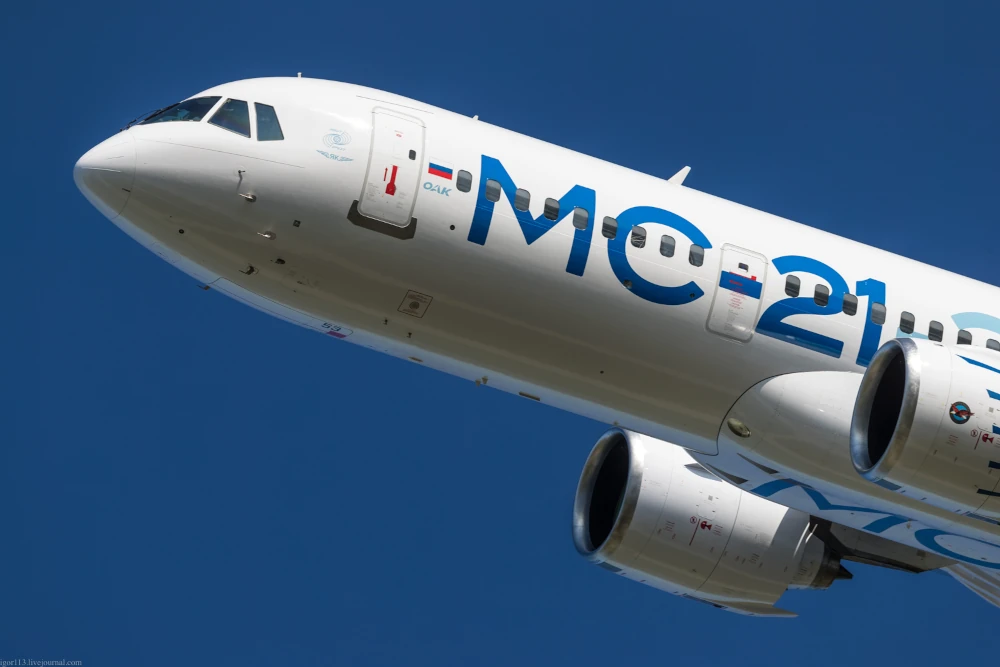
During the design and development of the PD-14, a great number of unique and sophisticated technologies were developed and implemented, including 16 critical technologies that allowed the engine to achieve the intended performance. For example, all elements and modules of the gas-air path were created using three-dimensional aerodynamic design methods, and all design work was done on paperless technology.
The fan has wide-chord titanium blades. CIAM developed the calculation and design technique for such blades in 2000, and it was initially used in the fans of the SaM146 and D-436-148FM turbofan engines. The PD-14 blades are hollow and made with superplastic forming and diffusion bonding.
The high-pressure compressor blisks (with a pressure ratio of 17) in the first, second, and fifth stages are titanium alloy, while the disks in the sixth through eighth stages are a new generation nickel powder alloy. The combustion chamber components are built of heat-resistant intermetallic alloy, with low-emission combustion via airblast atomizers and second-generation ceramic thermal barrier coatings. The high-pressure turbine blades and nozzle vanes are made of the most advanced single-crystal alloys VZhM4/5, which are protected by ceramic thermal barrier coatings, while the disks are composed of a new generation nickel alloy. The blades and vanes of the low-pressure turbine’s first through sixth stages are hollow and composed of titanium aluminide, with radial clearances actively controlled.
About 65% of the nacelle structure is made of composite materials. The nacelle is outfitted with a grid-type thrust reverser with electromechanical drive.
The PD-14 will be certified with thrust ratings of 123-137 kN for two MS-21 aircraft variants: the MS-21-300 (163-211 seats) and the MS-21-200 (132-165 seats). A lesser thrust variant of the MS-21-200 can be created by simply reprogramming the engine’s electrical controller.
The PD-14 is designed in such a way that modular engine repairs can be performed while the aircraft is still in service. This element also helps to shorten maintenance time in factory settings.
The PD-14 is not the only engine in its thrust class; it will face at least two main competitors: the PW1000G and the LEAP-1.
Comparing the PD-14 to its counterparts, the LEAP-1 and PW1000G is a challenging undertaking. These engines have very comparable performance, with mass differences of roughly 1.5-2.5%, thrust variations of 2-5%, and specific fuel consumption fluctuations of no more than 2%. These engines employ comparable materials and technologies.
The PD-14 gas generator consumes 12-15% more air than the PW1431G. This could indicate that the developer plans to use it in more powerful versions (such as the PD-14M and PD-18, which have thrust ratings of 15.6-18 tons). The bypass ratio chosen for the PD-14 is 8.5, which is lower than that of the competition. However, lowering the fan diameter by 8-15 cm does not significantly reduce the aerodynamic drag of the PD-14’s nacelle. This is especially true considering that the nacelle of the baseline engine for the MC-21 aircraft, the PW1431G, fits well beneath its wing and has adequate clearance from the runway surface.
The PD-14 combustion chamber warrants special attention. While it significantly outperforms the similar component in the PS-90A, it falls short of its competitors, who use second-generation dual-annular combustion chambers (TALON-X in the PW1000G and TAPS II in the LEAP-1). As a result, the PD-14’s emissions margins in compliance with ICAO Annex 16 will most likely be achieved only in cruise mode.
According to A.A. Inozemtsev, the PD-14 is not inferior to its overseas counterparts. One of the PD-14’s advantages is that it has a lower gas temperature at the turbine inlet (by 60-80°C), which results in a loss of thrust but saves energy during operation. Representatives of the Irkut Corporation believe that the PD-14 has 2.5-3% lower operating expenses than its competitors.
The PD-14 represents a considerable step forward for Russian aviation engine manufacturing, bringing it closer to, but not topping, Western technology. The PD-14 falls behind its competitors in production volumes and operational readiness by approximately 6-7 years. However, given the pandemic’s reduced demand for aircraft, this gap is less critical. At this point, it is critical to start delivering fast and gain the trust of the airlines.
The PD-14 is often referred to as the “locomotive” of progress, which is undeniably accurate. A significant amount of work has been accomplished: a new aviation engine has been designed, manufactured, tested, and prepared for serial production, resulting in employment creation at dozens of businesses and the development and mastery of advanced technologies and materials. Based on the PD-14 gas generator, work has begun on engines in smaller (PD-7, PD-10) and larger (PD-35) sizes, which Russia undoubtedly requires.
Everything appeared to be going smoothly until February 24, 2022. Following the outbreak of the war in Ukraine and the following sanctions imposed by the United States and the European Union, the MC-21 was left with only one engine option—the PD-14—and a local Russian market to service.